April 25, 2021
2 Types of Extrusion in HDPE Blow Molding
Extrusion Blow Molding is a widely known and used process for manufacturing plastic products (most commonly HDPE), from small volumes of 100ml up to large products of 1000L and more. This technique consists in the extrusion of a softened hollow thermoplastic, which is then blow molded and cooled in a mold until it solidifies and forms the final plastic product.
Some of the most popular product examples made by Extrusion Blow Molding are: Plastic bottles for household products, lubricant oil bottles, cosmetic bottles, jerry cans for edible oils, automotive parts, water tanks and drums for chemical liquids.
What are the Types of Extrusion Systems in HDPE Blow Molding?
There are 2 types of Extrusion systems in HDPE Blow Molding, which are:
• Continuous Extrusion
• Non-continuous Extrusion (with an Accumulator Head)
How can we know which HDPE Extrusion system is adequate for the product that will be made?
The key is in the size and weight of the product, and the amount of HDPE material necessary to produce it, this is called the shot size. The shot size is the length and weight of the Parison that will be ejected from the extrusion die head of the Blow Molding Machine.
In a Continuous Extrusion Blow Molding system, as the Parison is extruded continuously during the blowing cycles, the product’s weight and size should not be too big, as it will require a larger shot size and can make it difficult to control that the temperature of the bottom and top of the Parison remains constant.
In a Non-Continuous Extrusion Blow Molding system, the melted HDPE plastic material is first accumulated into a chamber in an Accumulator Head, it is then vertically extruded between 2 clamping plates in a single shot with high injection speed, then the 2 clamping plates close, and the blowing cycle begins.
At the time of calculating the shot size, it is extremely important to consider not only the dimensions and weight of the plastic product, but also the flasher. The flasher is the excess plastic that remains in the product after the blow molding process is finished and the plastic product is formed and taken out of the mold.
In this article, we will give a general introduction about the Non-Continuous type of Extrusion HDPE Blow Molding: the industries that benefit from this technology, the applications, the advantages of using an Accumulator Head, and some examples of these machines.
Non-Continuous Type of Extrusion: Accumulator Head HDPE Blow Molding Machines
First, it is important to know what these types of Extrusion Blow Molding Machines are called: Accumulator Head Blow Molding Machines.
Moreover, some of the main industries that benefit from Accumulator HDPE Blow Molding and the products that can be made with this technology are:
• Automotive (Air ducts and different HVAC system ducts)
• Household products (Tables, Seats, Baby Potty, HDPE Water tanks, PC Water Tanks)
• Industrial (Open top drums, L ring drums for chemical liquids, IBC tanks, Floats for Solar Panels, Packing vessels)
• Fitness & Sports equipment (Basketball Hoop base, Stackable Steps).
READ ALSO : HDPE Blow Molding Application
Advantages of Using Accumulator Head Blow Molding Machines
A non-continuous type Blow Molding Machine (Accumulator Head Blow Molding Machine) has many advantages over a Continuous type Blow Molding Machine when it comes to producing high quality large hollow plastic products, some of them are:
1. Better Control of the Parison Temperature. When the mold is ready to close, the plastic Parison is ejected at once and the blowing cycle can start, this means that the Parison does not have to be kept outside for a long time, and therefore, its temperature remains constant along all the points of the Parison, resulting in a high-quality product.
2. Increased Strength of the Production. As the die head can stock the melted plastic material, a two heart-shape flow channel can be designed for the plastic flow inside the die head, this design allows a weld line-free extrusion, which increases the strength of the production.
3. Stronger Clamping Force. The structural design of the Accumulator type Blow Molding machines allows the clamping unit to have a stronger clamping force, this force is equally distributed along the clamping plates, avoiding any air leaking during the product formation.
Examples of HDPE Blow Molding Machine with Accumulator Head
As customers' production demands become higher, we are challenged to step up our machines' designs and production cycle times, without compromising our so renowned efficiency and good quality. Thanks to our team of Engineers and specialty technicians, we have managed to achieve this goal in many of our most recently manufactured Blow Molding machines, thus, improving overall performance.
One example is our latest Double L Ring Drum making machine, with production ranges from 200L to 250L, with this machine, we have achieved a faster Injection Speed and Mold close-open movement, therefore, reducing the cycle time by 5 to 6 seconds!
Furthermore, our customers can also increase the strength of the HDPE drums for the drop test standards, by adding a Post Cooling Unit, especially designed for the narrow mouth 200L to 250L Double L Ring HDPE drum. Due to its high cooling capacity, it cools down the drum again and helps to complete its formation with an enhanced strength.
READ ALSO : Blow Molding HDPE Drums
Where are our Accumulator Head Blow Molding Machines installed Worldwide?
Our Accumulator Head Blow Molding machines have already been running for our customers for many years, the most popular are for Industrial applications like Air Ducts, Double L Ring, Open Top drums, Water Tanks and Floats for factories in Taiwan, Japan, India, United Arab Emirates, Egypt, Indonesia, Vietnam, and Philippines.
In addition, some other applications for smaller products like 30L jerry cans, ice cooler box, and 5 gallons PC water jugs in Malaysia, USA as well as in Taiwan; and some special plastic products like clothes mannequins for factories in South America.
READ ALSO : Blow Molding Machines Installation in Dubai and India during COVID-19 times.
For more information about Blow Molding Machines, please contact with us at:
E-mail : [email protected]
Some of the most popular product examples made by Extrusion Blow Molding are: Plastic bottles for household products, lubricant oil bottles, cosmetic bottles, jerry cans for edible oils, automotive parts, water tanks and drums for chemical liquids.
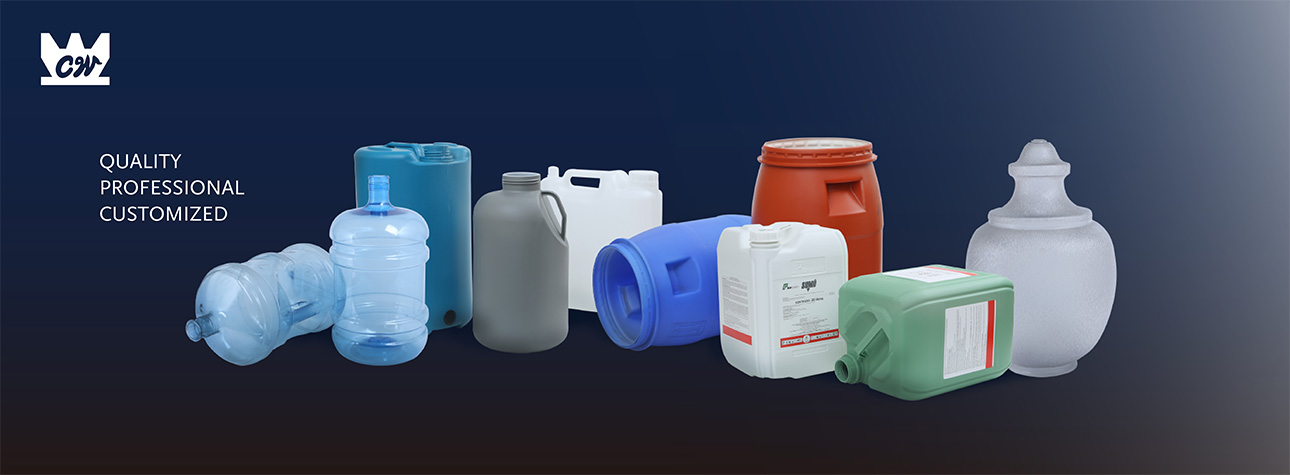
What are the Types of Extrusion Systems in HDPE Blow Molding?
There are 2 types of Extrusion systems in HDPE Blow Molding, which are:
• Continuous Extrusion
• Non-continuous Extrusion (with an Accumulator Head)
How can we know which HDPE Extrusion system is adequate for the product that will be made?
The key is in the size and weight of the product, and the amount of HDPE material necessary to produce it, this is called the shot size. The shot size is the length and weight of the Parison that will be ejected from the extrusion die head of the Blow Molding Machine.
In a Continuous Extrusion Blow Molding system, as the Parison is extruded continuously during the blowing cycles, the product’s weight and size should not be too big, as it will require a larger shot size and can make it difficult to control that the temperature of the bottom and top of the Parison remains constant.
In a Non-Continuous Extrusion Blow Molding system, the melted HDPE plastic material is first accumulated into a chamber in an Accumulator Head, it is then vertically extruded between 2 clamping plates in a single shot with high injection speed, then the 2 clamping plates close, and the blowing cycle begins.
At the time of calculating the shot size, it is extremely important to consider not only the dimensions and weight of the plastic product, but also the flasher. The flasher is the excess plastic that remains in the product after the blow molding process is finished and the plastic product is formed and taken out of the mold.
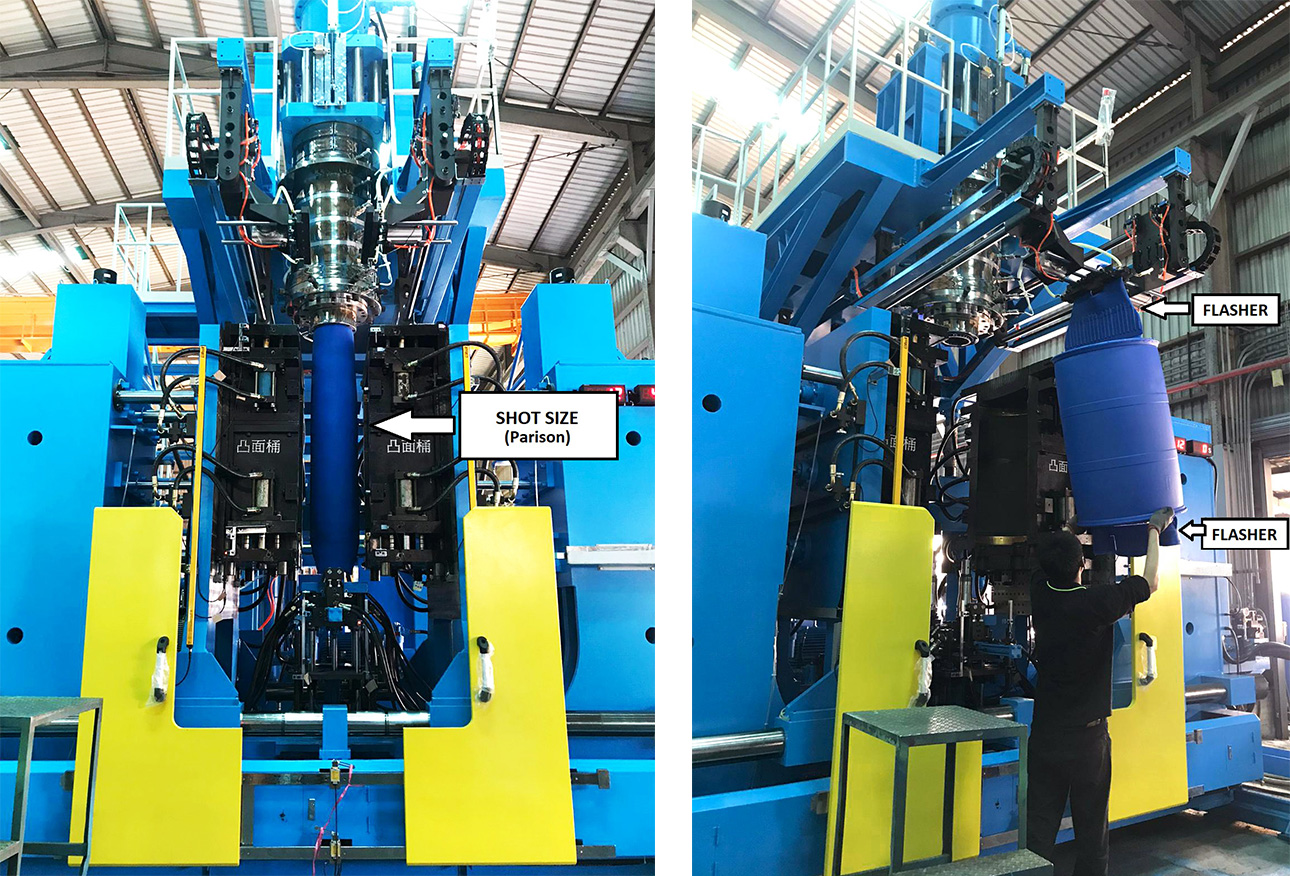
In this article, we will give a general introduction about the Non-Continuous type of Extrusion HDPE Blow Molding: the industries that benefit from this technology, the applications, the advantages of using an Accumulator Head, and some examples of these machines.
Non-Continuous Type of Extrusion: Accumulator Head HDPE Blow Molding Machines
First, it is important to know what these types of Extrusion Blow Molding Machines are called: Accumulator Head Blow Molding Machines.
Moreover, some of the main industries that benefit from Accumulator HDPE Blow Molding and the products that can be made with this technology are:
• Automotive (Air ducts and different HVAC system ducts)
• Household products (Tables, Seats, Baby Potty, HDPE Water tanks, PC Water Tanks)
• Industrial (Open top drums, L ring drums for chemical liquids, IBC tanks, Floats for Solar Panels, Packing vessels)
• Fitness & Sports equipment (Basketball Hoop base, Stackable Steps).
READ ALSO : HDPE Blow Molding Application
Advantages of Using Accumulator Head Blow Molding Machines
A non-continuous type Blow Molding Machine (Accumulator Head Blow Molding Machine) has many advantages over a Continuous type Blow Molding Machine when it comes to producing high quality large hollow plastic products, some of them are:
1. Better Control of the Parison Temperature. When the mold is ready to close, the plastic Parison is ejected at once and the blowing cycle can start, this means that the Parison does not have to be kept outside for a long time, and therefore, its temperature remains constant along all the points of the Parison, resulting in a high-quality product.
2. Increased Strength of the Production. As the die head can stock the melted plastic material, a two heart-shape flow channel can be designed for the plastic flow inside the die head, this design allows a weld line-free extrusion, which increases the strength of the production.
3. Stronger Clamping Force. The structural design of the Accumulator type Blow Molding machines allows the clamping unit to have a stronger clamping force, this force is equally distributed along the clamping plates, avoiding any air leaking during the product formation.
Examples of HDPE Blow Molding Machine with Accumulator Head
As customers' production demands become higher, we are challenged to step up our machines' designs and production cycle times, without compromising our so renowned efficiency and good quality. Thanks to our team of Engineers and specialty technicians, we have managed to achieve this goal in many of our most recently manufactured Blow Molding machines, thus, improving overall performance.
One example is our latest Double L Ring Drum making machine, with production ranges from 200L to 250L, with this machine, we have achieved a faster Injection Speed and Mold close-open movement, therefore, reducing the cycle time by 5 to 6 seconds!
Furthermore, our customers can also increase the strength of the HDPE drums for the drop test standards, by adding a Post Cooling Unit, especially designed for the narrow mouth 200L to 250L Double L Ring HDPE drum. Due to its high cooling capacity, it cools down the drum again and helps to complete its formation with an enhanced strength.
READ ALSO : Blow Molding HDPE Drums
Where are our Accumulator Head Blow Molding Machines installed Worldwide?
Our Accumulator Head Blow Molding machines have already been running for our customers for many years, the most popular are for Industrial applications like Air Ducts, Double L Ring, Open Top drums, Water Tanks and Floats for factories in Taiwan, Japan, India, United Arab Emirates, Egypt, Indonesia, Vietnam, and Philippines.
In addition, some other applications for smaller products like 30L jerry cans, ice cooler box, and 5 gallons PC water jugs in Malaysia, USA as well as in Taiwan; and some special plastic products like clothes mannequins for factories in South America.
READ ALSO : Blow Molding Machines Installation in Dubai and India during COVID-19 times.
For more information about Blow Molding Machines, please contact with us at:
E-mail : [email protected]

TOP