What is a Fully Automated Blow Molding Machine?
Importance of automation in extrusion blow molding
Evidence suggests that the future of work will be noticeably different from our jobs today. In the case of big blow molding businesses, many consider that automatic blow molding machines are not a luxury but a necessity to ensure continued success. Fully automatic blow molding machines’ main advantage is the reduction of manpower need which also translates to reduced costs, increased efficiency, and time savings. In other words, bottles, jerry cans, drums, and other plastic products can be produced in a shorter time with minimal human intervention.
Following the COVID-19 pandemic, it is also evident that businesses that are more agile, cost-efficient, and offer better customer and employee satisfaction are the ones that will continue to thrive, backing up the idea of the importance of automation.
How can a machine be fully automated?
A Continuous Extrusion Blow Molding Machine is fully automated when the machine includes an auto-deflashing unit and is integrated by a conveyor system with its auxiliary equipment. The auxiliary equipment for blow molding automation can be a conveyor, following a crusher or grinder for the recycling material, a mixer, a post-cooling unit, and a leak tester. The results are blow-molded products made by requiring less workforce or manpower.
Read more about automatic blow molding.
The automatic blow molding process
After the blow-molded product exits the
mold, the auto-deflashing unit removes the excess material. A conveyor system then
transports this waste material to the crusher, and the resulting grinded
material travels to the mixer and is automatically deposited into the bags,
ready to be reused.
In the case of 20L HDPE jerry can blow
molding machine, which is a popular choice for edible oil applications, it
commonly uses a top blow unit. However, some applications require the blow molding
machine to be suitable for producing outer thread HDPE jerry cans as well as
inner thread HDPE jerry cans. When this is the case, the machine will have a
bottom blow unit instead of a top blow unit, allowing the Blow Pin to be
interchangeable in order to incorporate an Unscrew Function to the blowing
unit, and properly form the inner threads in the neck of the jerry can.
Now, if this type of machine is to be integrated with a post-cooling and leak tester unit to obtain the finished product in an automized process, as the jerry can is upside down, it needs to be turned over and moved into the conveyor system to complete the production line. For this process to be performed, our Blow Molding machine includes a suction and turn-over unit that carefully transfers the jerry can to the post-cooling and leak tester section of the machine.
Chen Way Machinery: machine testing video of automatic blow
molding machine with auto-deflashing and suction & turn-over unit for jerry
cans
Chen Way Machinery’s automatic blow molding machines
At Chen Way Machinery our team is always in the good disposition to work with you and find the most suitable solution to your demands. Because every client needs a different solution for their specific products, we customize our blow molding machines in order to meet these needs and provide the most efficient, practical, and economical solution. This also implies that every machine's design of the automatic processes for a complete production will vary according to the shape of the bottle, jerry can, drum or any hollow product that is being blow molded.
Chen Way Machinery: machine testing video of automatic blow molding machine with view stripe, auto-deflashing unit, and leak tester.

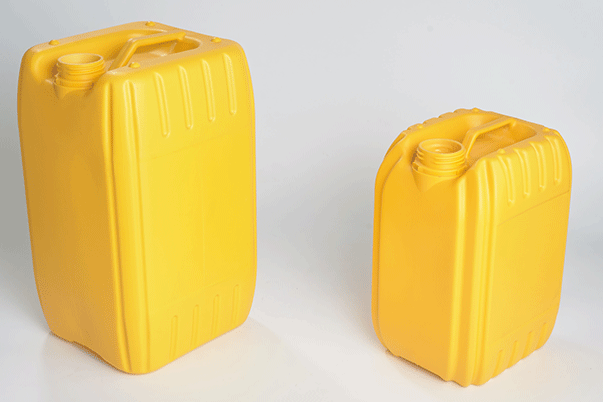
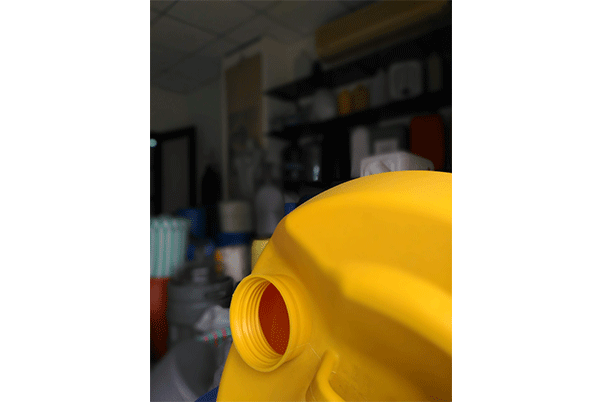

TOP