Nov 21, 2024
What Factors Affect the Quality of Products in Extrusion Blow Molding?
The Importance of Quality in Extrusion Blow Molding
Extrusion blow molding (EBM) serves as the backbone for producing a wide range of essential products—HDPE chemical drums, edible oil jerry cans, beverage bottles, pharmaceutical containers, and more. Celebrated for its cost-effectiveness and robust output, EBM remains a dominant method in high-quality, durable plastic production.This guide explores the key factors influencing product quality in EBM and provides actionable insights for optimizing production outcomes.
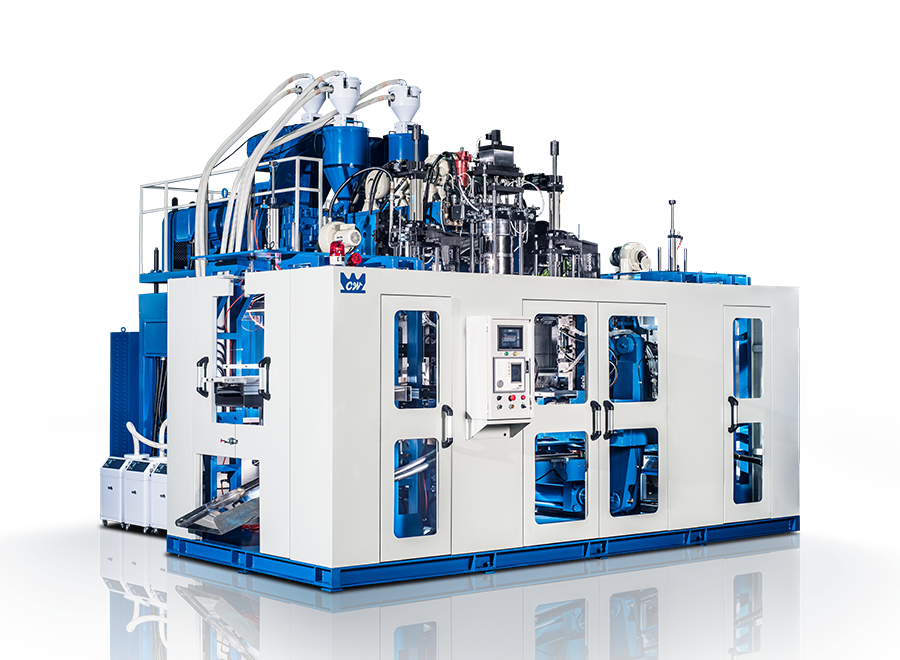
1. Material Selection and Its Impact on Quality
- Choosing the Right Polymer The cornerstone of successful extrusion blow molding lies in material selection. Common materials include:
- HDPE (High-Density Polyethylene):Valued for strength and chemical resistance.
- LDPE (Low-Density Polyethylene):Offers flexibility but lower structural rigidity.
- PETG (Polyethylene Terephthalate Glycol):Balances clarity and impact resistance.
- PP (Polypropylene):Lightweight, resistant to heat and chemicals, making it ideal for products requiring high thermal stability, such as food containers and automotive components. Choosing the wrong material can lead to defects such as warping or Aligning polymer selection with application requirements is essential for quality results.
- Additives and Colorants Additives such as stabilizers and colorants impact both appearance and performance. Improper use can compromise material properties and result in defects.
- Material Purity High-purity resins are critical for consistent quality. Contaminated or recycled resins may introduce inconsistencies and visible flaws.
- Melt Temperature Control Melt temperature significantly influences product consistency. Fluctuations can lead to uneven wall thickness and reduced structural integrity. Steady melt temperatures ensure uniform wall distribution.
- Extrusion Speed and Pressure Balanced extrusion speed and pressure are crucial for even material flow. High speeds may thin the material excessively, while low speeds can create thicker, uneven sections.
- Parison Programming Advanced parison programming minimizes waste and ensures uniform wall thickness, reducing the risk of shape inconsistencies.
- Precision of Mold Construction High-precision molds are vital for consistent product quality. Accurate molds minimize defects and maintain product shapes.
- Mold Cooling System Efficiency An efficient cooling system impacts product surface quality and dimensional stability. Poor cooling can result in warping and surface defects.
- Material Flow Within the Mold A well-designed mold supports smooth material flow, reducing risks of warping and uneven surfaces.
- Calibration and Machine Settings Regular calibration ensures consistent output. Incorrect settings can cause product variation and defects.
- Preventative Maintenance Routine maintenance prevents unexpected breakdowns and helps sustain product quality. Ensuring all machine components function correctly is essential.
- Role of Automation and Monitoring Systems Modern machines with sensors and real-time monitoring can detect and adjust issues, maintaining high precision. Industry 4.0 technology, including AI-based predictive maintenance, enhances production reliability.
- Ambient Temperature and Humidity Temperature and humidity in the production environment can affect cooling and solidification. Climate-controlled areas support consistent quality.
- Cleanroom Requirements for Certain Applications Medical or food-grade container production may require cleanroom conditions to prevent contamination.
- In-Line Quality Checks Ongoing checks, such as wall thickness measurements and visual inspections, catch defects during production.
- Post-Production Testing Durability, stress resistance, and leak prevention tests confirm products meet quality standards.
- Data Analysis and Continuous Improvement Analyzing quality data enables process refinement and supports long-term production improvements.
- Leakage Leakage often results from poor welding or contamination. Precise mold matching and well-designed blow pin nozzles help prevent it.
- Rocker Bottoms Insufficient cooling before removal can lead to unstable bottoms. Improved cooling water flow and clean channels can resolve this.
- Tearing of Welding Lines High mold closing speeds or thin parison sections may cause welding line tears. Adjusting mold speed and increasing parison thickness at critical points mitigates this.
- Surface Wall Defects Defects like black spots, streaks, and ripples can stem from contamination or moisture. A hopper dryer can prevent moisture-related bubbles, while gradual parison adjustments avert ring-like lines.
- Uneven Radial Wall Thickness This defect, leading to shrinkage, can be corrected by aligning the die mandrel and reducing pre-blow.
- Finish Trim Defects Inadequate clamping force or cooling can cause trimming issues. Ensuring proper mold size and closure helps prevent these defects.
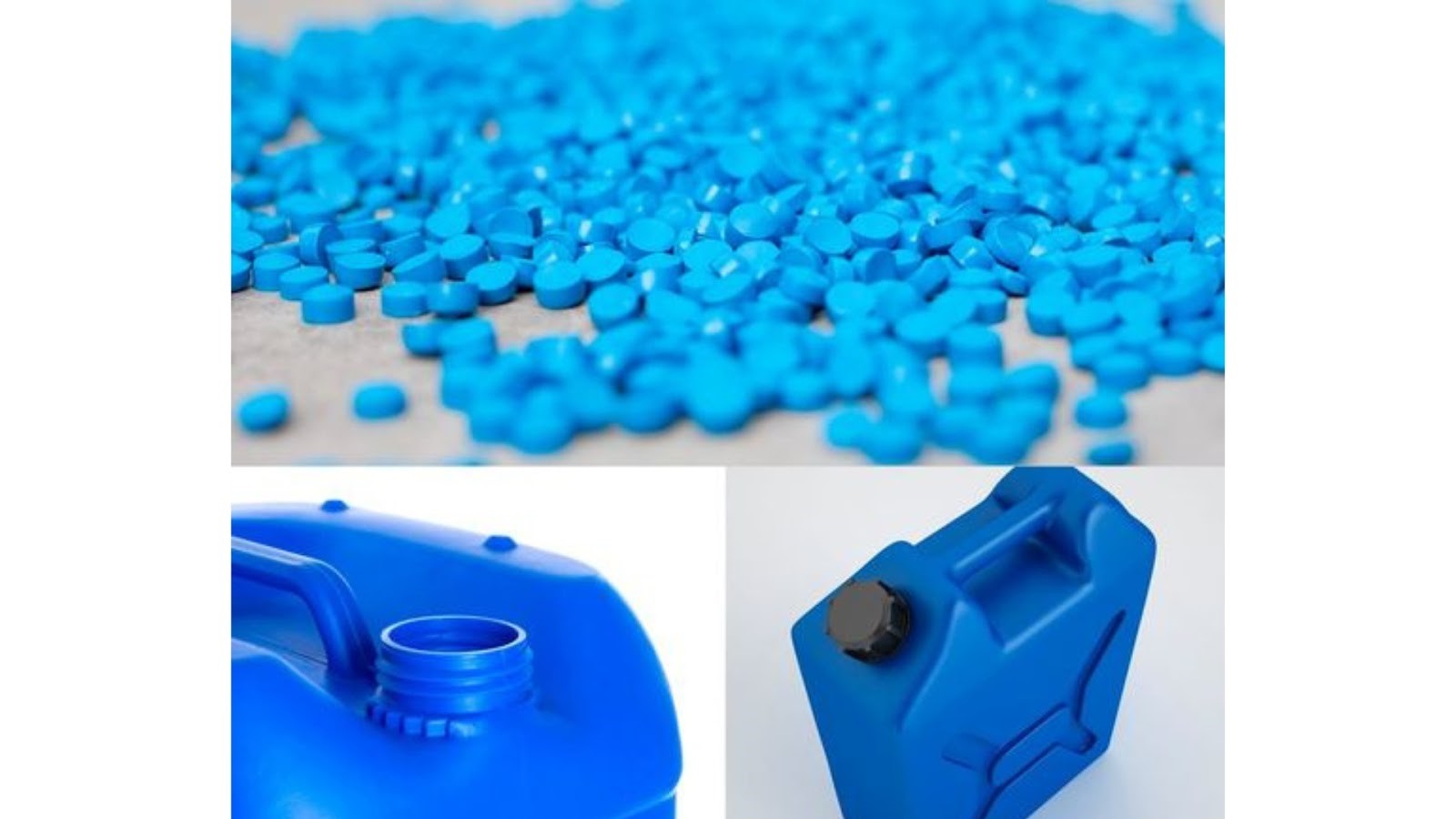
2. Extrusion Parameters and Their Effect on Product Consistency
3. Mold Design and Quality Considerations
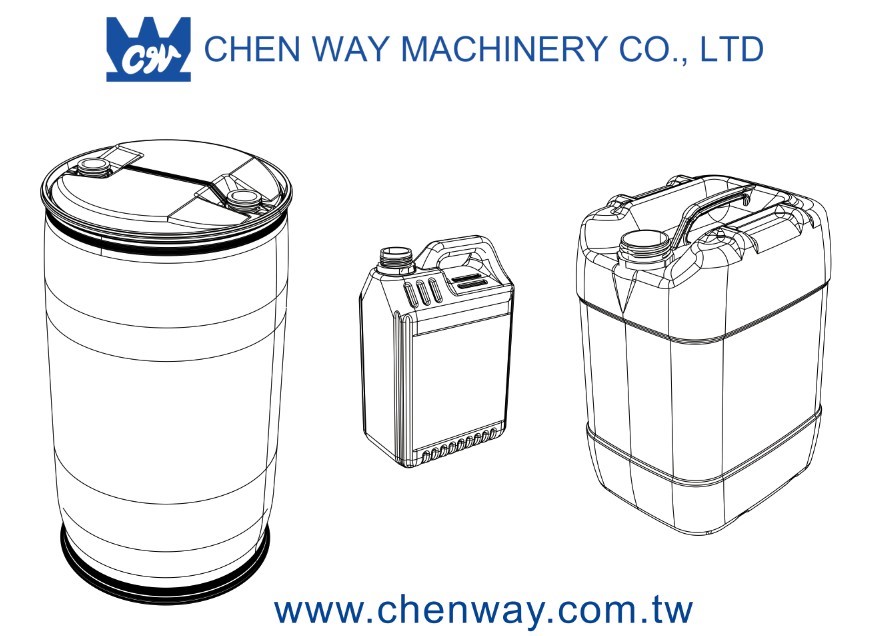
4. Machine Setup and Maintenance
Read more:What is a Fully Automated Blow Molding Machine?
5. Environmental Factors That Can Influence Product Quality
Read more:Highly Efficient Clean Room Blow Molding for Pharmaceutical Bottles and Containers
6. Quality Control and Testing Procedures
7. Common Defects and How to Prevent Them
Read more:Blow Molding Troubleshooting Guide - Top 6 Problems
Customized Solutions by Chen Way Machinery
At Chen Way, we understand that no two production lines are the same. This is why we specialize in providing tailored solutions that meet specific client requirements. Our team works closely with each client to develop machines that are optimized for their unique production needs, whether they require handling multi-layer structures, integrating recycled content, or adapting to bioresin processing.Chen Way's engineering expertise allows for the customization of components such as extruder barrels, screws, and mold plates to ensure seamless performance, even with challenging materials like PHA. Our commitment to innovation is showcased through machines equipped with advanced monitoring systems, allowing for real-time data collection and analysis to optimize performance and maintain product quality.
Whether you need an upgrade to incorporate eco-friendly practices or seek automation solutions to boost productivity, Chen Way offers reliable, state-of-the-art technology. From consultation to implementation, we guide our clients through every step, ensuring they achieve efficient and sustainable production processes.
Case Study: Enhancing Production for Jerry Cans and Chemical Containers
A leading manufacturer in Kenya approached Chen Way with a need for improved efficiency in producing jerry cans and chemical containers. Their existing machinery was facing issues like inconsistent wall thickness and leakage. Chen Way provided a customized EBM solution that included advanced parison programming and upgraded mold cooling systems. These improvements resulted in products with more uniform wall distribution and reduced defect rates. Additionally, the integration of real-time monitoring systems allowed for quick adjustments, minimizing downtime.The client reported a 20% increase in production output and a significant reduction in material waste, demonstrating Chen Way’s commitment to providing practical, high-quality solutions tailored to customer needs.
Achieving High-Quality Extrusion Blow Molding Products
Consistent product quality in extrusion blow molding depends on attention to detail in material selection, machine setup, and environmental conditions. Incorporating sustainable practices, such as using bioresins and advanced machine technology, is increasingly essential. Chen Way’s advanced technology and proven expertise make us the preferred partner for reliable, high-performance EBM solutions.For more information, explore How HDPE Extrusion Blow Molding Machines Work for Jerry Can Production in Kenya, which highlights practical applications and innovative solutions in specific markets. Additionally, learn 3 Must-Know Tips to Cost Saving and Ecofriendly Blow Molding to maximize efficiency and support environmental goals.
Ready to enhance your blow molding process? Contact Chen Way for expert consultation and customized solutions.
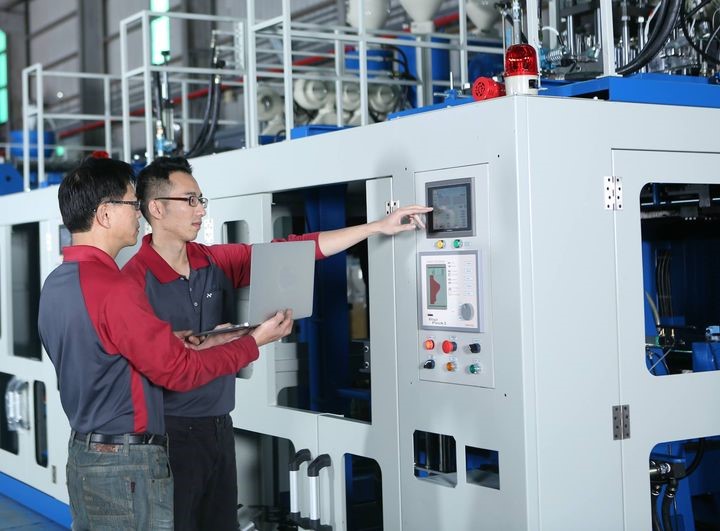

TOP